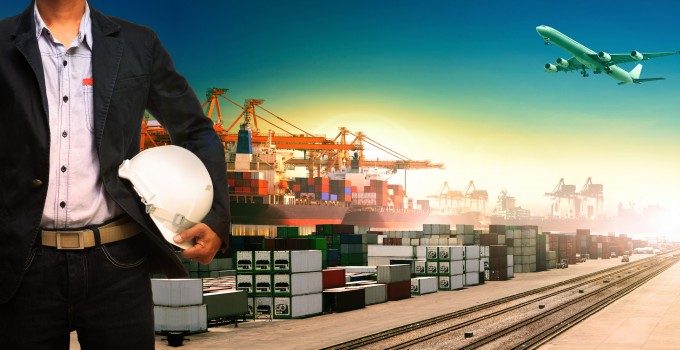
Some of the world’s biggest logistics companies – and even the United Nations – are still struggling against criminal gangs supplying counterfeit refrigerant gas to the cool supply chain.
And in this never-ending battle with the bootleggers, the latest weapon appears to be a spreadsheet.
A new ...
Comment on this article