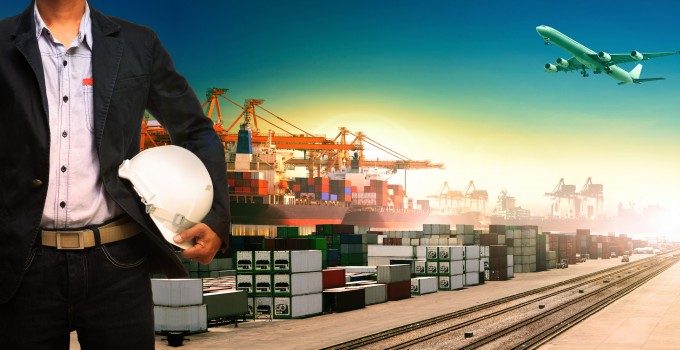
© Khunaspix Dreamstime.
Shipping lines could save millions of dollars in fuel costs if time spent in ports was decreased by even the most marginal amounts, claims new analysis from container shipping consultancy SeaIntel.
The company, in conjunction with industry group the Global Institute of Logistics and software provider ...
Comment on this article
Kevin monteath
November 28, 2012 at 2:32 pmWith the ships getting bigger, and the old system of joint service, this time saving will not be possible at ports. The shipping giants need to address these points of port services in respective countries. Bigger and more containers, and joint service with partners bring in more cargo, hence the port authorities need to understand this and bunker cost. I am sure the pencil can be sharpened to save shipping lines millions of dollars… My views..
Mike Harrison
January 03, 2013 at 5:18 pmIf you want to save time when berthing, the pilot and master must have confidence in the approach manoeuvre, should know the permitted berthing speeds and angles of the installed fenders, and have the right Portable Piloting Units (PPUs) to see the full picture. The cost is peanuts compared to the savings on more efficient operations. At Inshore Systems we advise clients on reducing risks and cost without compromise.
Perhaps container lines should consider equipping pilots with PPUs as well as reviewing the fenders on the berths they use. Small investments will pay large dividends.
Ted Daly
March 28, 2013 at 12:28 pmThe real savings comes about by evaluating and determining the best schedule to keep for the entire round trip voyage of the vessel. While I agree pilot time and maneuvering are two critical components of a port stay, many times there is little to no opportunities to save enough time to justify slow steaming unless you have a good amount of pilotage time, considered over 2 hours in duration. Most pilots and vessel captains work hand in hand to get the vessel quickly to the dock, as long as the weather conditions allow for that safe transit. So it is hard to find more time there.
The real savings comes at the dock. Vessel clearance by authorities can take up to 2 hours in some locations. Stevedoring time or the production and the number of gangs put on the vessel upon arrival also is a contributing factor. With ever larger move counts and larger vessels stowage planners need to know each port limitations intimately and make sure the vessel is stowed in the most efficient manner to allow for the most gangs and best productivity, decreasing the total port time. As an example, with a move count is 3,500 and 4 gangs to total port stay would be 35 hours, at 25 GMPH/Gang. With the same move count and production with 6 gangs you can save almost 12 hours of port time. This can be a more realistic and sustainable time savings opportunity than just saving 30 min of pilot time or maneuvering time at a few ports of call. Manage to save this kind of time over 8 to 10 port calls and you can save up to 120 hours per round trip, that is 5 days saved, now that is a significant amount of time and the vessel could then save money by slow steaming. Roll it all together, stevedoring time saved, reduce time in port, better pilot times, slow steaming and you can make a significant impact on the overall cost of operating a vessel.
Rick Eyerdam
April 09, 2013 at 3:34 pmGreat comments. Tideworks Technology among others can improve the loading/off-loading configuration and some scheduling. Ted is right on but he needs to take it to the next step in the logistics chain gang. Are there enough roadworthy chassis, TWIC empowered truck drivers, or space to store containers that must wait days for a move? When does demurrage kick in? Are the gates fast enough – in and out — and what about the highways?
Then there are the train intersection issues. In short fast cranes and agile gangs are essential unless the fill the yard so fast the cargo is bogged by its own time-sensitive volume.
These are some of the issues we are trying to reduce to the least common denominator as part of the stand up of the Caribbean Maritime Exchange.